A – Operations Management and the Organizations
- Operations Management – the transformation of ‘inputs’ into ‘outputs’ that meet the needs of the customer.
- Operations Strategy – common strategies involve what is known as the value chain and supply chain management.
- Sustainability in operations management – Sustainability is a long-term programme involving a series of sustainable development
B - Quality Management
- The scope of quality management
- Quality management approaches
- Total quality management (TQM)
- Managing quality using TQM
- Processes of continuous improvement
- Lean production
- International Organization for Standardization (ISO)
- Total productive maintenance (TPM)
- The TQMEX Model
- Service quality
- Capacity management
- Balancing capacity and demand
- Capacity planning
- Capacity control
- Inventory management
- Just-in-time (JIT)
Operations Management – the transformation of ‘inputs’ into ‘outputs’ that meet the needs of the customer.
The Operations Function – the core function includes the following: (Code: MOP)
M –Marketing and sales – identifying customer needs
O – Operations – fulfilling customer orders and requests through production of the goods or services.
P – Product and service development – designing new products and services that will meet customer needs
Mintzberg’s Operating Core -- Henry Mintzberg suggested five parts of looking at organizations. (Code: ATOMS)
A – Strategic Apex or Finance Director/Manager
T – Technostructure or Human Resource Managers
O – Operating core or Operators
M – Middle line or the Supervisors
S – Support Staff or ISS
The transformation process model – could be a physical transformation, a change in nature or form, a change in location, a change in ownership or psychological changes
Operations Strategy – common strategies involve what is known as the value chain and supply chain management.
The Value Chain – sequence of business activities by which, in the perspective of the end-user, value is added to the products or services produced by an entity.
Business activities are not the same as business functions
Primary Activities (Code: LOOMS)
L – Inbound Logistics
O – Operations
O – Outbound Logistics
M – Marketing and sales
S – After –sales services
Secondary Activities (Code: TRIP)
T – Technology development
R – Human Resource management
I – Firm Infrastructure
P – Procurement
The Value System – is the set of value chains to achieve competitive advantage
Purchasing and supply chain management – concerned with the flow of goods and services through the organization with the aim of making the firm more competitive.
Reck and Long – identified the four-phased development of purchasing within organizations. (Code: IPIS)
I - Independent
P - Passive
I - Integrative
S – Supportive
Cousins – investigate the level of strategic maturity in the purchasing function of UK/European companies. (Code: SARCASM)
S – Skills
A – And Competences
R – Portfolio of Relationships
C – Corporate and Supply Strategy
A – Cost/Benefit Analysis
S – Organization structure
M – Performance Measures
Supply chain networks – interconnecting group of organizations which relate to each other through linkages between the different processes and activities involved in producing products/services to the ultimate customer.
Demand Networks – recent evolution of supply chains. Supply chain is formed to ‘push’ the product out into the market. Demand Networks are ‘pulled’ into existence to demand signals.
Four-stage process (RACO)
R – Reacting
A – Anticipating. Six Sigma
C – Collaborating. External relationships
O – Orchestrating. Flow of information
To create competitive advantage, organizations within a demand network have to manage THREE FACTORS: 3A’S
A – Alignment – of shared incentives
A – Agility – to respond to demand quickly
A – Adaptability – to adjust the structure of the supply chain to meet demand
Supply portfolios and sourcing strategies
Single – the buyer chooses one source of supply
Multiple – the buyer chooses several sources of supply
Delegated – a supplier is given responsibility for the delivery of a complete sub-assembly. For example, rather than dealing with several suppliers a ‘first-tier’ supplier would be appointed to deliver a complete sub-assembly.
Parallel – mixing/combining the other three approaches to maximize the benefits of each.
Process Mapping – aims to identify and represent the steps and decisions involved in a process, in diagrammatic form
Types of process maps:
- Basic flowchart – basic ‘birds eye’ view
- Deployment flowchart – overview and indicates where or by whom actions are performed. This includes a ‘department’ or ‘unit’ dimension along the top of the chart.
O – Structure of Operations
N – New products/services
C – Capability required
R – Range and location of operations
I – Investment in Technology
B – Buyer-supplier relationships
Sustainability in operations management – Sustainability is a long-term programme involving a series of sustainable development
Efficiency – reducing waste, using less energy and recycling
Stakeholder support – reducing greenhouse gas emissions, employee cycle schemes, employee flexible working
Market edge – innovation, supply chain improvements, R&D
B – Quality Management
The scope of quality management
Quality – totality of features and characteristics of a product or service which bears on its ability to meet stated or implied needs
M – Quality Management. This is concerned with controlling activities with the aim of ensuring that products or services are fit for their purpose and meet specifications.
A – Quality Assurance. This focuses on the way a product or service is produced.
C – Quality Control. This is concerned with checking and reviewing work that has been done.
Quality management approaches
SERVQUAL – by Zeithaml, Parasuraman and Berry in 1980s; method of measuring quality in service organizations. To measure the gap between a customers preconceived expectations and the actual experience they receive
(Code: Rater)
R – Reliability. Service dependably and accurately
A – Assurance. Inspire confidence and trust in the customer
T – Tangibles. The tangible environment, like facilities, equipment and staff appearance
E – Empathy. Caring and Personal service is provided
R – Responsiveness. Willingness to help and respond to customer requests
The Balanced Scorecard – by Kaplan and Norton (1990). Quality measures should cover operational, financial and customer aspects.
(Code: I CFO)
I – Innovation and Learning
C – Customer
F – Financial
O – Operational: Internal Operations
Value of money audits – involves identifying and measuring key aspects of performance, such as money spend, inputs purchased, outputs and outcomes achieved.
Total quality management (TQM) – aims to continuously improve quality in all aspects of the organization. Customer satisfaction is key objective of TQM.
TQM is the continuous improvement in quality, productivity and effectiveness obtained by establishing management responsibility for processes as well as output.
a. Deming – decrease in process variability will increase quality and productivity
b. Ouchi (Theory Z) – devised by William Ouch in the early 1980s.
B – Building relationships
I – Interpersonal skills
G – Group interaction and decision-making
P – Participative management
A --
R – Retention of hierarchical rules and control
T -- Trust
S – Formal procedures for planning and setting objectives
c. Juran (Fitness for use) – quality should focus on the role of the customer, both internal and external.
d. Ishikawa (Quality circles) – stressed the importance of people and participation to improve quality.
e. Crosby (Quality costs) – worker participation and the need to motivate individuals to do something about quality.
f. The elements of TQM – (CODE: PRECEPT)
P – Prevention. Prevent poor quality
R – Right first time. Develop a culture that encourages workers to get their work right first time.
E – Eliminate waste. Most efficient and effective use of all its resources
C – Continuous improvement. Kaizen philosophy
E – Everyone’s concern.
P – Participation. Workers should share their views and the organization should value them
T – Teamwork and empowerment. Form team bonds to become one.
Managing quality using TQM
TQM promotes the concept of internal customer and internal supplier, which some requires SLA – Service Level Agreement. This is a statement of the standard of service and supply that will be provided to the internal customer and will cover issues such as the range of services supplied, response times, dependability and so on.
Kaizen – or the continuous improvement, looks for uninterrupted incremental change.
Principles of continuous improvement: CARNAGE
C – Changing customer needs
A – Assets are the people in the organization
R --
N – New technologies
A – Alignment on resources, measurements, rewards and incentives
G – Gradual improvement
E – Evaluation (statistical/qualitative) should be the basis of improvement
Quality of costs (Code: A PIE)
A – Appraisal/inspection Cost. Cost incurred after a product has been made or service delivered
P – Prevention Cost. Cost prior to making the product or delivering the service
I – Internal Failure Cost. Cost from inadequate quality before the transfer of the item to customer
E – External Failure Cost. Cost from inadequate quality after the transfer of the item to customer
TQM Philosophy (CODE: QUEZON)
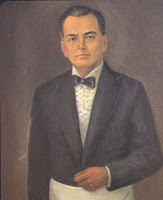
U – Unacceptable
E – Estimated seriously the failure cost
Z – Zero defects
O – Optimal quality level
N – No further challenge to management to improve quality further
Failure of TQM (CODE: RC LTD)
R – Rejection
C – Cynicism
L – Lack of management buy-in
T – Tail-off
D – Deflection
Processes of continuous improvement
Quality circles – is a team of workers from within organization which meets at intervals to discuss issues relating to the quality of the product or service produced
Benefits of Quality Circles (Code: MUSIC)
M – Morale of employees improves
U – Unity in organization is fostered as the circle includes all levels
S – Savings should materialize
I – Improvement/solutions are likely, as workers know the process involved
C – Culture of quality
Drawbacks of Quality Circles (Code: RIPE)
R – Rejected suggestions may cause resentment
I – Influence can be very wide
P – Power is hard to control
E – Eg cost, business practicalities many not be fully understood
The 5s – (lean production), there is a place for everything and everything goes in its place
Six Sigma – near perfect products and services. This is customer focused, rather than operations oriented. Looks at critical outcomes that affect customer satisfaction.
Lean production – Toyota Production System. This is the philosophy of production that aims to minimize the amount of resources used in all activities. Identify and eliminate non-value-adding activities
International Organization for Standardization (ISO)
a. ISO 9001:2000 – ISO’s current quality management system requirements (to be registered)
b. ISO 9000:2000 and ISO 9004:2000 – ISO’s quality management system guidelines
c. ISO 19011 – covers quality auditing standards
d. ISO 14001 – relates to environmental management systems
ISO 9000 certified or registered – an independent registrar has audited their processes and certified that they meet the ISO requirements
ISO 9000 compliant – met ISO’s quality system requirements, but have not been formally certified by an independent registrar. It is a self-certified.
Total productive maintenance (TPM) – the productive maintenance carried out by all employees through small group activities
Five goals of TPM (Code: TAIPE)
T – Train all staff in maintenance skills
A – Autonomous maintenance
I – Improve equipment effectiveness
P – Plan maintenance
E – Early equipment management
Benefits of TPM (Code: BUCAO)
B – Breakdowns are reduced
U – Uniform output and production consistency
C – Cost of quality and reduction in waste
A – Accuracy of production schedules is improved
O – On time delivery
The TQMEX Model – understand the relationship between quality management and other aspects of operations management.
BPR – Business Process Re-engineering is the rethinking and radical redesign of business processes to achieve dramatic improvements in critical contemporary measures of performance, such as cost, quality, service and speed.
Four themes of BPR (C A R P)
C – Creative use of IT
A – Ambition
R – Rules are broken and challenged
P – Process reorientation
Five phases of BPR (P I E R I)
P – Planning
I – Internal learning
E – External learning
R – Redesign
I – Implementation
Service quality – measure quality in service organizations by reference to customer expectation. This is the totality of features and characteristics of that service which bears on its ability to meet stated or implied needs.
Service quality factors (CHEN)
C – Critical factors
H – Hygiene factors
E – Enhancing factors
N – Neutral factors
C – Managing Capacity and Inventory
Capacity management
Capacity – measure of what an operation is able to produce within a specified period of time.
a. Overcapacity – resources are available for production are not fully utilized
b. Undercapacity – more production is being demanded than is able to be produced
Balancing capacity and demand
Four planning and control activities
L – Loading. This is the amount of work that is allocated to an operating unit.
S – Sequencing. The order in which different jobs will be done or different orders fulfilled.
S – Scheduling. Detailed Timetable
M – Monitoring and controlling. Work is proceeding as planned
Push control – pushing work through each stage of the process
Pull control – calling for work to be delivered from the previous process when it is needed.
Capacity planning – maximize profits and customer satisfaction
Capacity control
MRP I – (Materials requirement planning) technique for deciding the volume and timing of materials, in manufacturing conditions where there is dependent demand
MRP II – (Manufacturing Resources planning) plan for planning and monitoring all the resources of a manufacturing company: manufacturing, marketing, finance and engineering
OPT – (Optimized Production Technology) scheduling production that focuses on the known capacity constraints of the operation.
ERP – (Enterprise Resource Planning) like MRP II but uses databases from all parts of the organization.
Inventory management
Inventory control levels (MR MAR)
M – Minimum level, inventories are approaching a dangerously low level and the outages are possible
R – Reorder level, needs to replenish stocks
M – Maximum level, inventories are reaching the potentially wasteful level
A – Average inventory, inventory levels fluctuate evenly between the minimum inventory level
R – Reorder quantity, inventories reach the reorder level (EOQ)
Just-in-time (JIT) – goods and services should be produced only when they are needed
Characteristics in Operations required by JIT (FRESH)
F – Flexibility, respond immediately to customer orders
R – Reliability, not subject to hold-ups
E – Elimination of errors that brings lower costs
S – Speed, throughput should be past
H – High quality
Three Key Elements in JIT philosophy (ETC)
E – Elimination of Waste
T – The involvement of all staff in the operation
C – Continuous improvement/Kaizen
0 comments:
Post a Comment